أرسل لنا رسالة
iron ore grinding mill from italy
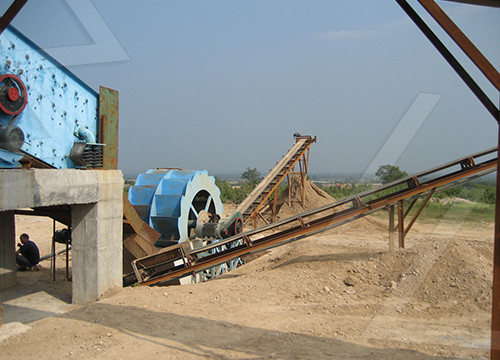
Comparing strategies for grinding itabirite iron ores in
2021315 Iron ore Itabirite Pilot plant milling Semi-autogenous grinding 1. Introduction High-grade iron ores from Brazil were frequently processed via multistage
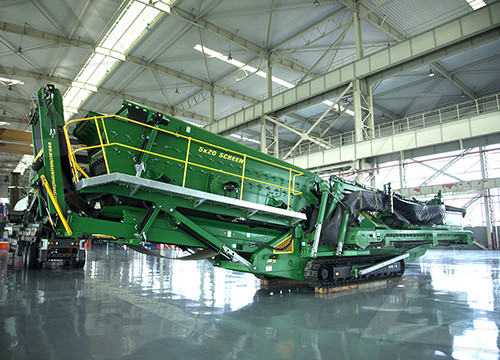
Vertical mill simulation applied to iron ores ScienceDirect
201541 In this study, a coarse sample of iron ore was tested in a pilot scale grinding circuit with a vertical mill. Other three samples of pellet feed had already been tested with
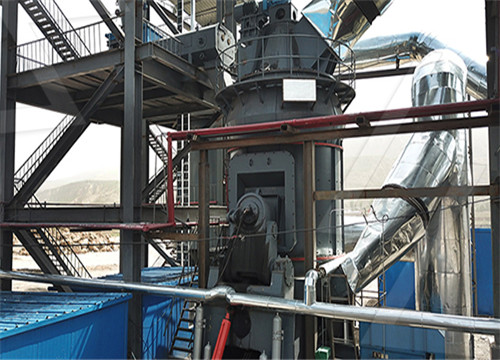
Grinding iron ore concentrate by using HPGR and ball mills
Read this article. An iron ore concentrate sample was ground separately in a pilot-scale HPGR mill in multiple passes and a dry open-circuit ball mill to increase the specific
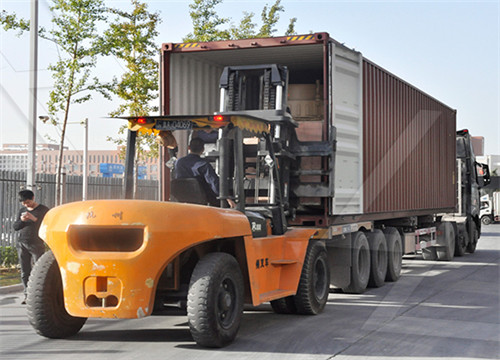
Investigation on Iron Ore Grinding based on Particle Size Distribution
2020528 In the iron and steel industry, the production of narrow particle size distribution (PSD) for pellet feed making with acceptable liberation of valuables from the
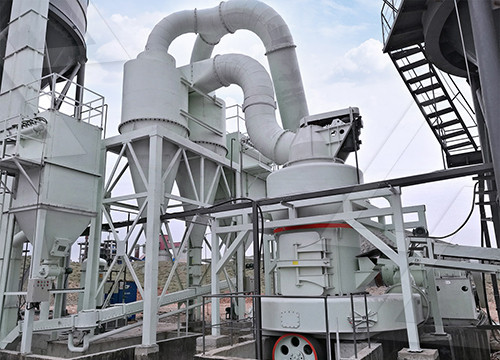
Research of iron ore grinding in a vertical-roller-mill
2015315 In case of the Kiruna ore there was the possibility to take samples of the concentration plant KA1 in Kiruna, while the same feed material was ground, as used for
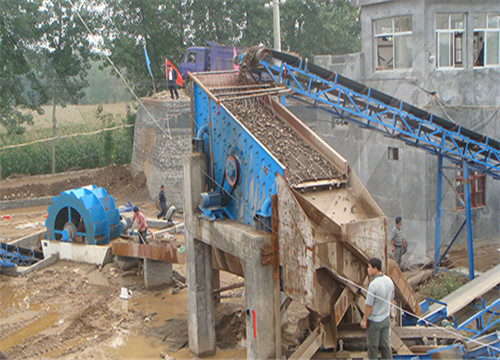
Metso to supply two energy efficient Vertimill® grinding mills to iron
2023922 A Canadian iron ore producer has awarded Metso an order for two powerful Vertimill® 4500 grinding mills to be delivered in Q3 of 2024. The value of the
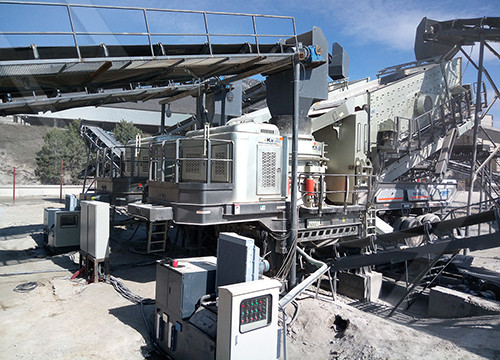
Optimization of Solids Concentration in Iron Ore Ball Milling
2019618 The present work analyzes comminution of a Brazilian iron ore with unusual breakage behavior in batch and pilot-scale tests, as well as in an industrial mill,
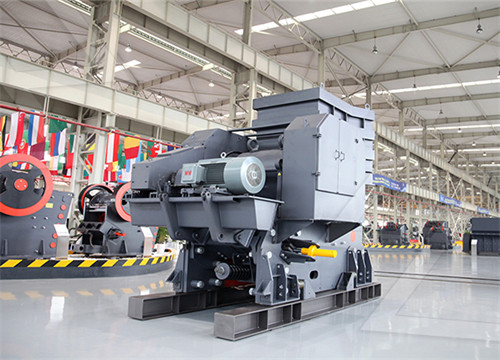
(PDF) Evaluation of grinding circuits for iron ore
201931 The aim of this study was to evaluate and compare two grinding circuits in an industrial iron ore plant, by evaluating the current operation through sampling,
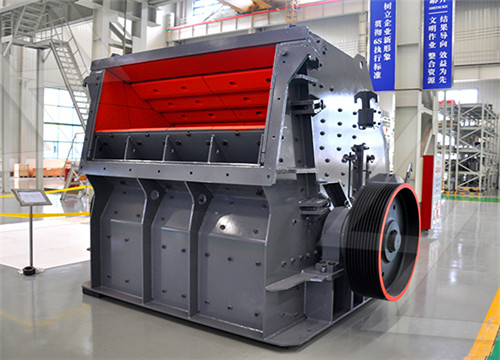
Mechanistic modeling and simulation of grinding iron ore
2021111 The present work analyzes the application of the UFRJ mechanistic ball mill model to grinding of iron ore pellet feed in an industrial grinding circuit. In order to
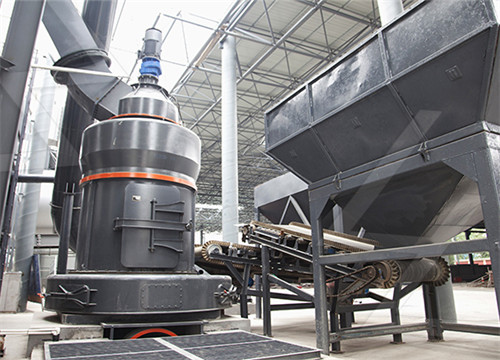
Avoided energy cost of producing minerals: The case of iron ore
2019111 Thus, the total specific energy for concentrating iron ore at the average ore grade (∼ 50% iron) from Thanatia (3.63% iron) was considered as the sum of the energy
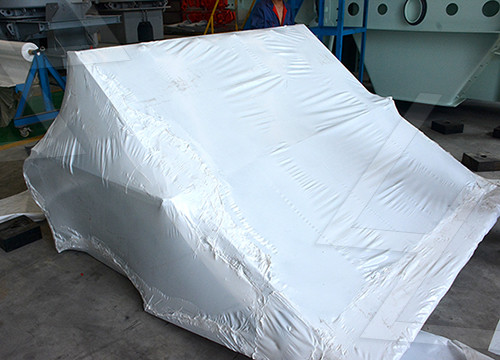
Research of iron ore grinding in a vertical-roller-mill
2015315 The application of vertical-roller-mills (VRM’s) for ore grinding is part of the second strategy. The grinding parts of a Loesche mill ( Fig. 1) are a rotating table (1) with a horizontal grinding track and rollers (2), which are pressed onto the table by lever arms and a hydro pneumatic spring system.
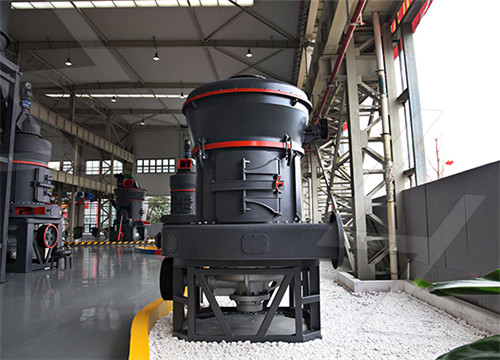
Developments in iron ore comminution and classification
201511 The Zourerat iron ore mine has two 1.7 m diameter × 1.8 m wide HPGR units treating 1400 t/h each of aerofall mill pebbles. The feed is − 25 + 1.6 mm and has a ball mill work index of 12–14 kWh/t. The iron ore has low to moderate abrasion characteristics. Figure 8.21 shows the Zourerat iron ore flowsheet.
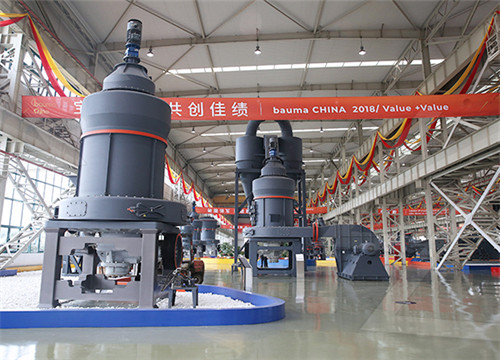
11.23 Taconite Ore Processing US EPA
2015910 The average iron content of pellets is 63 percent. 11.23.2 Process Description2-5,41 Processing of taconite consists of crushing and grinding the ore to liberate iron-bearing particles, concentrating the ore by separating the particles from the waste material (gangue), and pelletizing the iron ore concentrate.
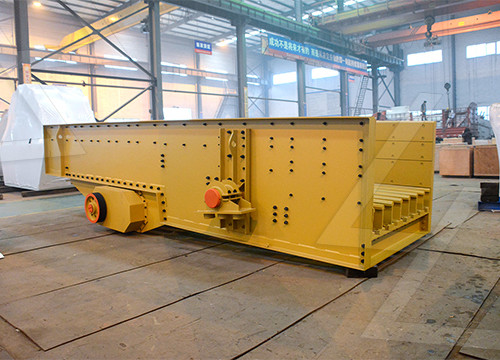
Energy and Environmental Profile of the U.S. Mining
2013118 Iron ore occurs naturally in a variety of forms, from sand-like iron fines to solid rock masses. Crude ore, or ore mined in the natural state, seldom occurs in a pure state and requires some form In the grinding circuit, rod, ball, or autogenous mills grind the taconite down into even smaller uniformed-sized particles. The ore is ground
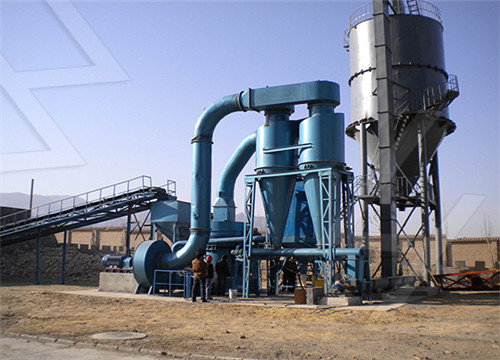
Comparing strategies for grinding itabirite iron ores in
2021315 In spite of the important advances in modelling and simulation of autogenous and semi-autogenous grinding made in recent decades (Napier-Munn et al., 1996, Morrell, 2004), risks exist in designing a circuit adopting AG/SAG mills for low-grade itabirite iron ores from bench-scale information.
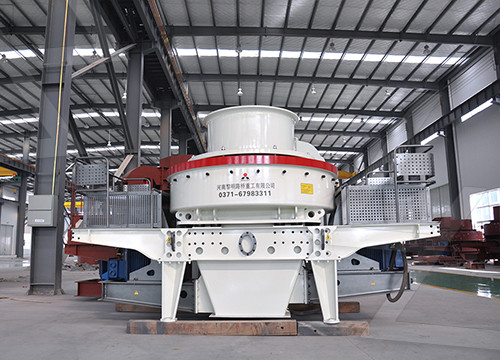
Process Mineralogical Assessment of the Grinding Products
2022112 Comminution tests with a laboratory-scale rod and ball mill of 13 predefined ore types from the Per Geijer iron oxide-apatite deposits were conducted. The grinding setup refers to the so-called Malmberget method used at LKAB, characterized by a subsequent circuit of rod and ball mill grinding.
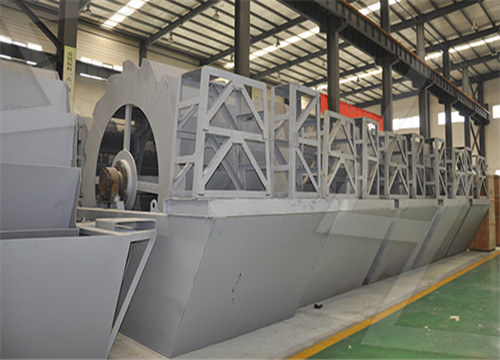
The Effect of Grinding Media on Mineral Breakage Properties
20211211 The mineral composition and content are shown in Table 1.According to the measurement result by MLA, the minerals in the ore were mainly magnetite and quartz, accounting for 32.48% and 61.73%, respectively, and their weight was accounted for 94.21% of the total, indicating that the magnetite ores can be basically considered a two
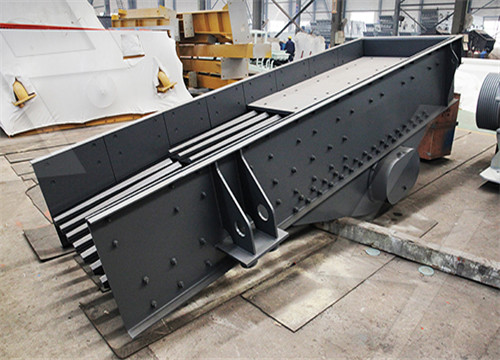
Operational parameters affecting the vertical roller mill
201741 Pilot plant test results with various ores showed that low energy consumption feature of vertical roller mills is applicable to the ore industry. Grinding test results for zinc ore showed that it is possible to decrease the total grinding energy consumption from 20.11 to 11.40 kW h/t by using vertical roller mill instead of AG/SAG
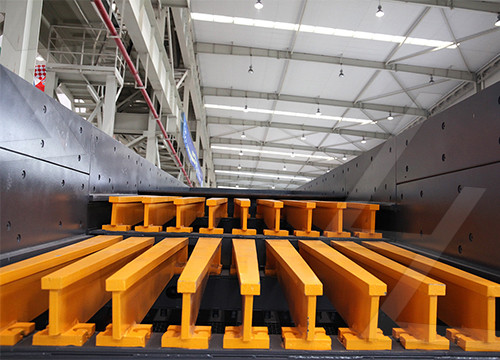
(PDF) Eco-Efficient and Cost-Effective Process Design for
2013916 Reducing Grinding Energy and Cost -Magnetite Iron Ore Design Case Study. Efficiency of the comminution operations is traditionally assessed based on operating cost and energy consumption
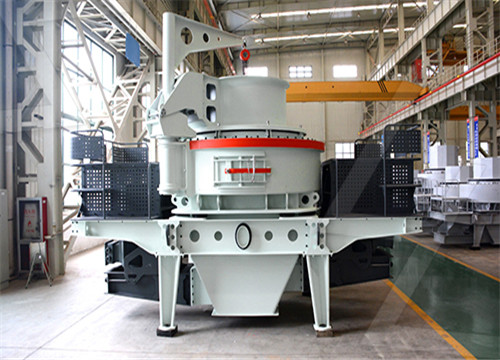
How much is a grinding mill in South Africa LinkedIn
2023227 The price of a grinding mill in South Africa depends on several factors, including the manufacturer, model, and size of the machine. For example, a small household grinding mill may cost around R2
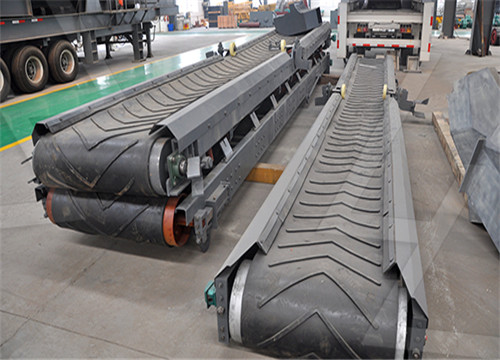
Development of a Novel Grinding Process to Iron Ore
2020328 2.1.2 Ore Blend Grinding at HPGR and Ball Mill. The ore blend was ground in a pilot-scale HPGR (1 m diameter × 0.32 m width) at a maximum feed rate of 50 t/h. The ground product was recirculated to the HPGR feeding hopper five or seven times, wherein every recirculation steps a sample was gathered for moisture and size distribution
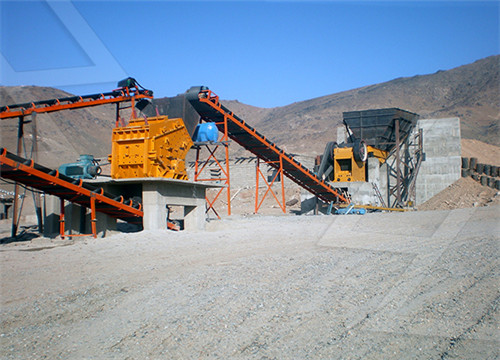
Iron Ore Processing, General SpringerLink
20221020 Iron ore handling, which may account for 20–50% of the total delivered cost of raw materials, covers the processes of transportation, storage, feeding, and washing of the ore en route to or during its various stages of treatment in the mill.. Since the physical state of iron ores in situ may range from friable, or even sandy materials, to monolithic
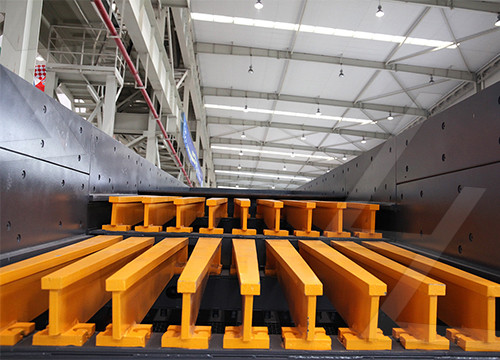
Study on Quantitative Separation Method of
202346 Based on batch grinding method and normalization idea, a conical ball mill is used and a quantitative separation method of grinding characteristics of multi-component complex ore is proposed. The results
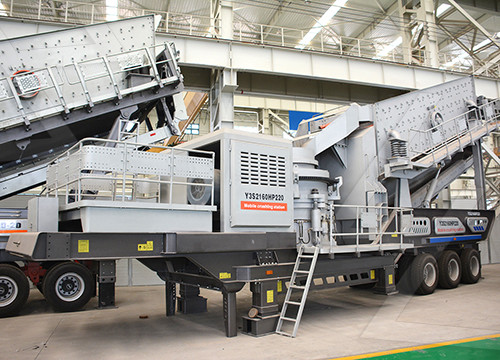
The six main steps of iron ore processing Multotec
3. Feeding the crusher (Reclaim) The surge pile allows a constant supply of material to be fed into the mill, which ensures consistent results and stability in the ore recovery process. 4. Grinding. The primary grinding mill grinds the material before it
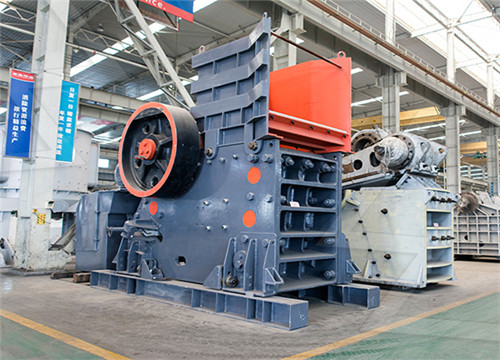
Estimation of Grinding Time for Desired Particle Size
202013 2.2 Grinding Studies. Two kinds of mills, BBM and LBM, were used to achieve the desired P 80 passing percentage of 150 μm with an acceptable range of hematite liberation (> 75%) at optimum grinding time. The BBM is a standard ball mill having a length and diameter of 300 mm × 300 mm with smooth liner as shown in Fig. 2.A
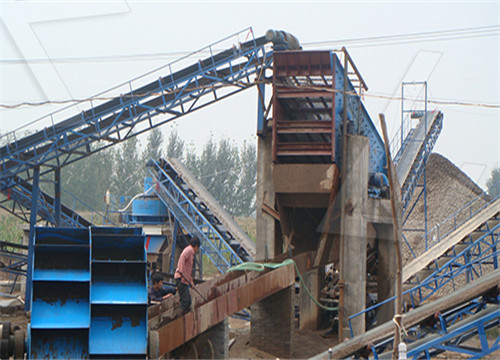
Trends in der Minenindustrie Mineral Processing
Today, HPGRs are some of the most important types of mill in the mining industry. From the market leader thyssenkrupp alone, so far more than 130 roller crushers have been sold for a range of different applications, such as grinding diamond ore/kimberlite, iron ore or iron ore concentrate and metal ores (hard rock).
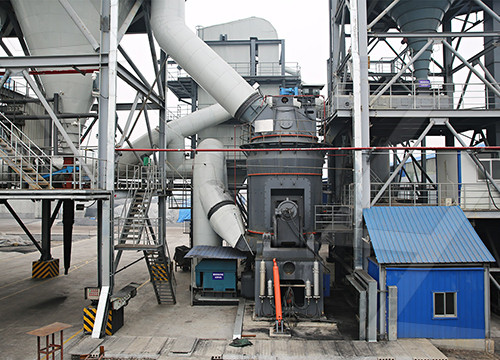
Processing Citic Pacific Mining
2023726 The conveyor carrying crushed ore from the mine to the concentrator area is 2.4m wide and 1.7km long. Sino Iron uses largest AG mills in the world, at 12.2m in diameter and 11m long with 28MW gearless motors. The ball mills, the second stage grinding equipment, are 7.9m in diameter and 13.6m long, each with two 7800 kW motors.
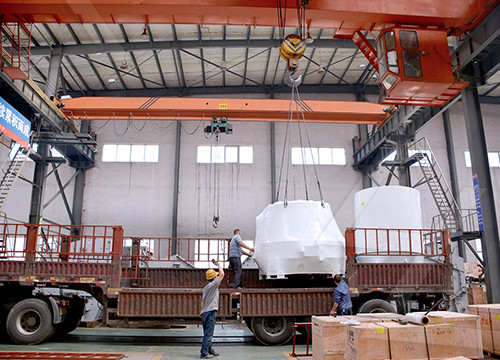
Energy Use of Fine Grinding in Mineral Processing SpringerLink
20131218 Fine grinding, to P80 sizes as low as 7 μm, is becoming increasingly important as mines treat ores with smaller liberation sizes. This grinding is typically done using stirred mills such as the Isamill or Stirred Media Detritor. While fine grinding consumes less energy than primary grinding, it can still account for a substantial part of a mill’s
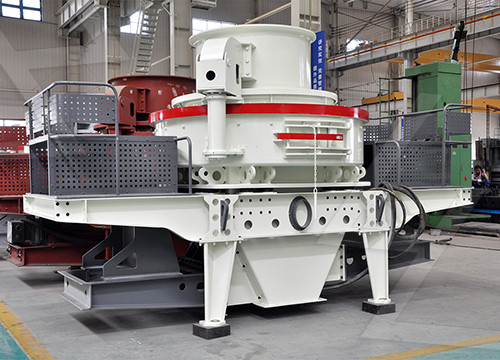
Mechanistic modeling and simulation of grinding iron ore
2021111 The present work analyzes the application of the UFRJ mechanistic ball mill model to grinding of iron ore pellet feed in an industrial grinding circuit. In order to address the challenge of applying the model to a reasonably fine feed, selected model parameters were back-calculated on the basis of batch grinding tests. The model is then