أرسل لنا رسالة
concentration measurement on ball mill silica
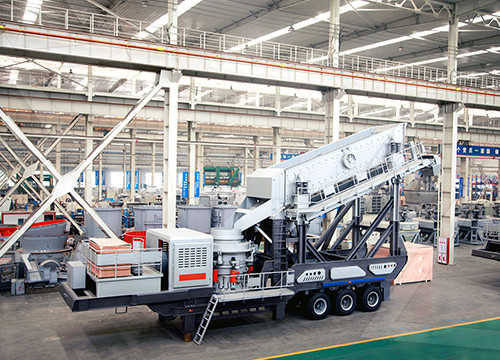
Comparative Study on Improving the Ball Mill Process
The optimum process parameters setting concluded that balls to powder weight ratio are 20:1, the optimum ball mill working capacity is 2 L while the optimum speed of the ball mill is 105 rpm. Using SEM characterization, the improved particles of silica sand presented a
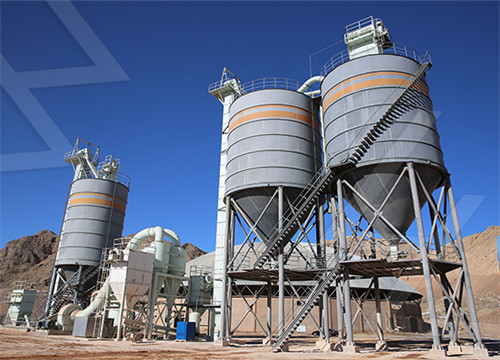
Parameter Optimization of Ball Milling Process for Silica
The three main parameters applied in this study are Ball to Powder weight Ratio (BPR), time milling process, and rotational speed (rpm). The materials used in the study was Bangka
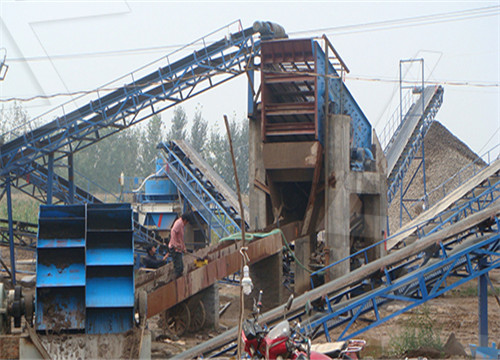
Surface modification of silica powder by mild ball milling
In this study, a catalyst- and solvent-free ball mill treatment was conducted to modify the silica powders by the mild ball milling process as the simple and the low manufacturing
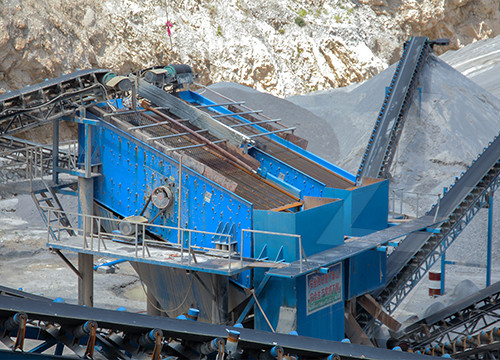
sbm concentration measurement on ball mill silica.md GitLab
M mill Project information Project information Activity Labels Members Repository Repository Files Commits Branches Tags Contributors Graph Compare Issues 0 Issues
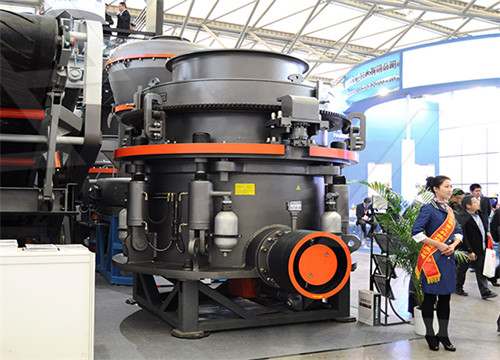
Two-Stage Continuous Process for the Extraction of Silica
This study developed a two-stage continuous silica extraction process from limestone husk using attrition ball milling and alkaline leaching methods. A continuous process has several
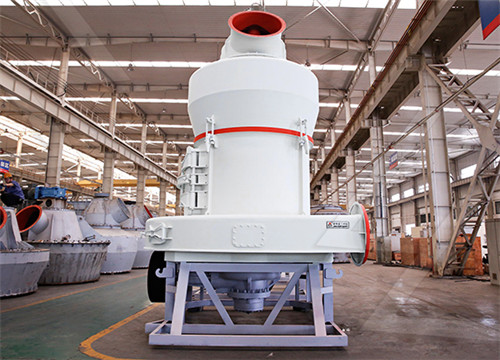
PAPER OPEN ACCESS Parameter Optimization of Ball
Parameter Optimization of Ball Milling Process for Silica Sand Tailing To cite this article: Sukanto et al 2019 IOP Conf. Ser.: Mater. Sci. Eng. 494 012073 View the article online
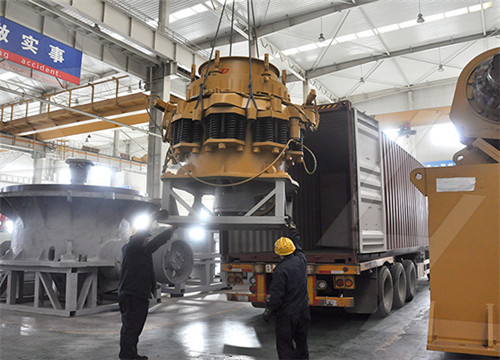
Silane pre-treated silica produced by ball milling and its
This work provided a good insight on the feasibility of producing a pre-treated silica through the industrial commonly applied ball milling method to disperse the silica agglomerates
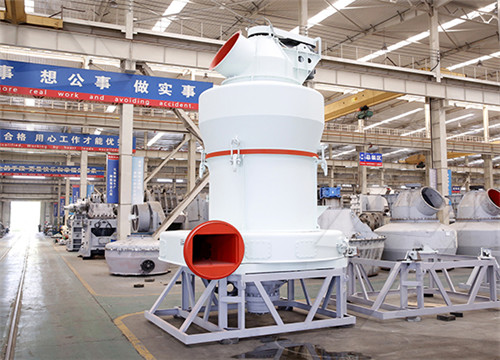
Silane pre-treated silica produced by ball milling and its
Pre-treated silica was prepared by ball milling the mixture of 60˚g precipitated silica, 72˚g TESPT and 480˚g acetone con-tained inside a concealed ball milling container of volume
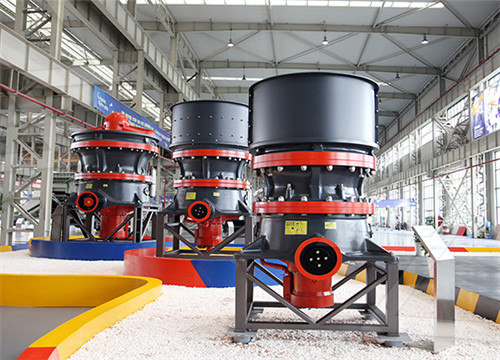
Particle filling and size effects on the ball load behaviour and
The ball load behaviour in a pilot mill is studied under conditions of increasing particle filling, for coarse silica feed (0.8–1.8 mm) and fine silica feed (0.075–0.3 mm), at the mill
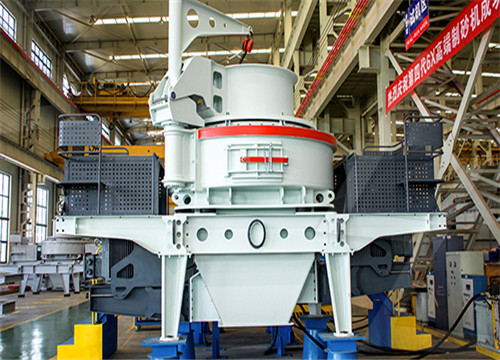
Evolution of grinding energy and particle size during dry ball
In this , we present a detailed investigation of the dry grinding of silica sand in an oscillatory ball mill. We are interested in the evolution of specific surface area (SSA),
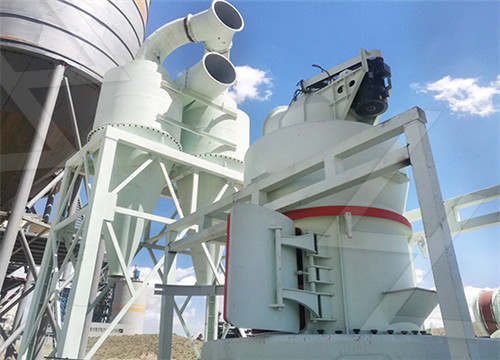
concentration measurement on ball mill silica
Subject Index ASTM International ball mill test, fig., 13 ball mill test with synthetic sea-water, fig., 15 Corrosivity, in limestone slurry scrubbers, 121-122 D Departure value, formulas, 163 Diaphragm pump, 248, fig., 250 Dry sand rubber wheel abrasion test, 38 E Electrical capacitance, pipeline ero sion measurement, 93 Energy approach, erosion
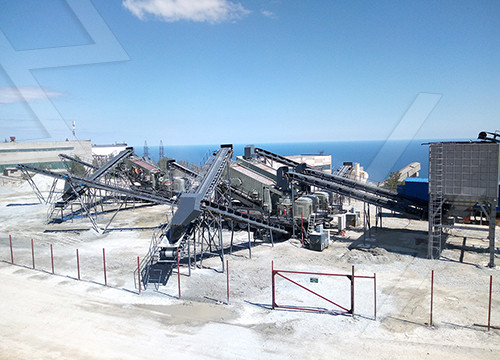
Minerals Free Full-Text Estimating Residence Time MDPI
2022128 This stone compares two deconvolution methodologies used to estimate residence time distributions (RTD) in industrial closed-circuit ball mills. Parametric and non-parametric deconvolution techniques were evaluated. Both techniques allowed for direct RTD estimates from inlet and outlet tracer measurements in the mills, with no need for
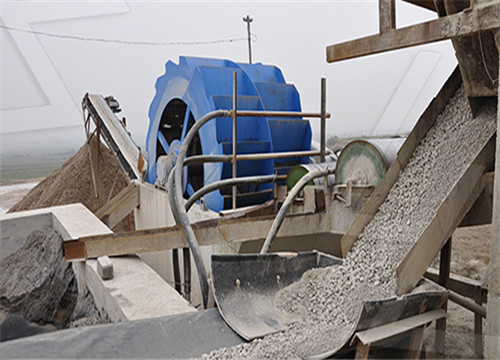
Ball Mill For Silica Crusher Made In Japan
Concentration Measurement On Ball Mill Silica. Silica Sand Ballmill Grinding . Silica Sand Ballmill Grinding. Ball Mill For Silica Grinding Made In Japan. In this study we conducted grinding tests on silica glass using a ball mill and measured the grind ing rate with the permission of the editorial committee of the Soc Powder Technology Japan
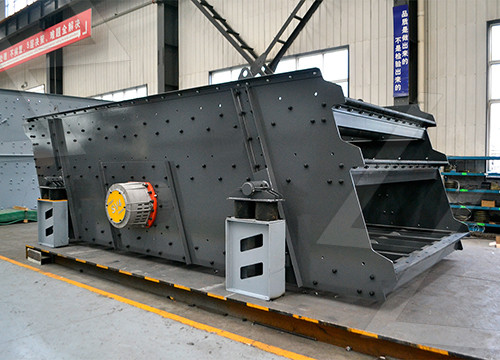
concentration measurement on ball mill silica
2022620 Ball And Concentration Mill ericmorvanarchitecte.fr. Ball And Concentration Mill. Ball Mill Ball Mill Manufacturer Ball Mill Machine. Ball Mill The ball mill is a key equipment to grind the crushed materials, and the ball mill is widely used in powder-making production line including cement, silicate, new-type building material, refractory
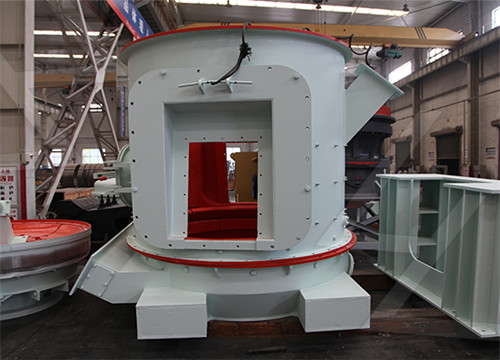
Silica Exposures in Artisanal Small-Scale Gold Mining in
2015814 PURPOSE. The purpose of this investigation was to measure respirable crystalline silica exposures among workers in ASGM in Tanzania. Because small-scale gold miners lack basic personal protective equipment and generally operate without any dust controls, it is important to assess their exposures separately from workers in medium and
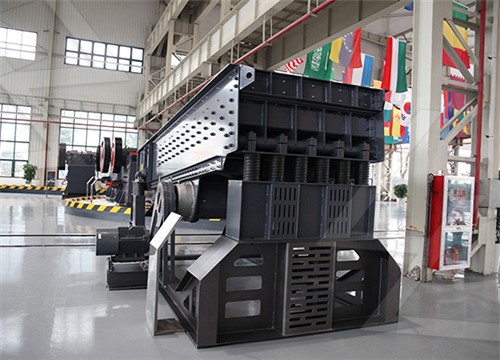
(PDF) Effect of ball and feed particle size distribution on the
201821 In another study to investigate ball size distribution on ball mill efficiency by Hlabangana et al. [50] using the attainable region technique on a silica ore by dry milling, a three-ball mix of
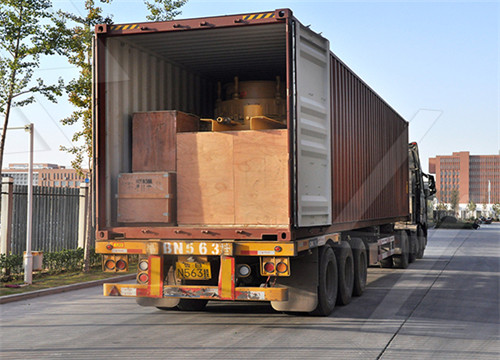
concentration measurement on ball mill silica
2020323 Amorphous silica powder was mechanically treated by a planetary ball mill system, by which the surface of powders was activated and simultaneously particle size reduced extensively. Surface of powders with different milling conditions was investigated by scanning electron microscopy (SEM) and nitrogen adsorption isotherm.
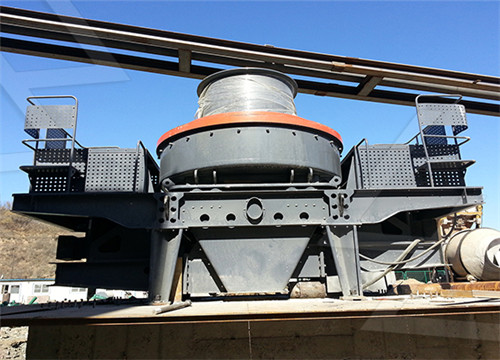
Raman spectroscopy for real-time and in situ monitoring of Nature
202164 This protocol describes how to set up and use Raman spectroscopy for monitoring the course of solid-state reactions in vibratory ball mills, which will help increase our understanding of the
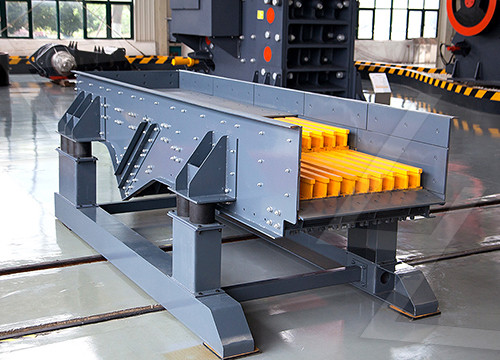
Particle filling and size effects on the ball load behaviour and
2008108 The ball load behaviour in a pilot mill is studied under conditions of increasing particle filling, for coarse silica feed (0.8–1.8 mm) and fine silica feed (0.075–0.3 mm), at the mill speeds of 63, 78, 88 and 98% of the critical.
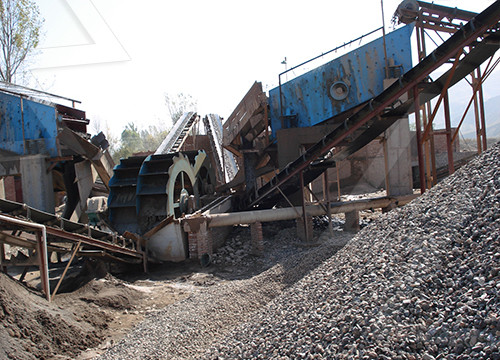
Mechanochemistry for ammonia synthesis under mild
20201214 The typical ball-mill rotation speeds were 250, 300, 350, 400, 450 and 500 r.p.m. 1/8 inch i.d., 2 mm o.d., HayeSep Q 80/100 µm) was used to measure the ammonia concentration in the gas
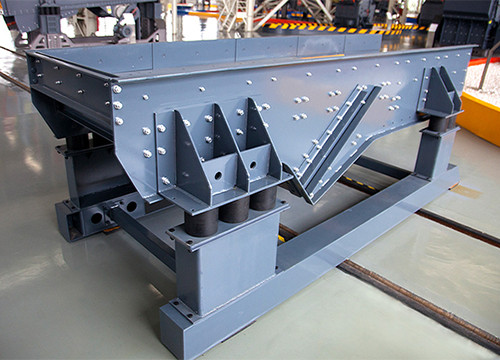
Eco-friendly strategy for preparation of high-purity silica
202381 An eco-friendly utilization strategy of high-silicon IOTs was proposed. • SiO 2 grade and recovery in quartz concentrate were 93.12% and 45.24%, respectively.. SiO 2 purity of high-grade silica reached 99.93% after three-stage acid leaching.. This study realizes the recycling and utilization of high-silicon IOTs.
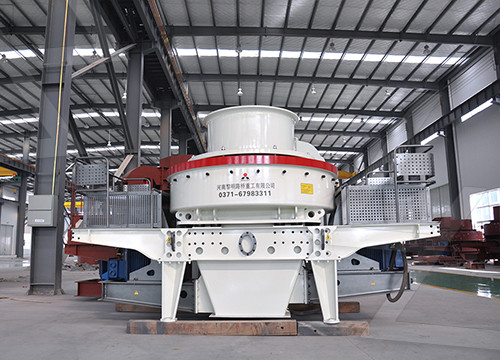
Synthesis and application of limestone husk silica nanoparticles for
2020111 A two-stage ball milling process was used to reduce the particles to nano size. A planetary ball mill machine DECO-PBM-V-2L-A; DECO, China containing a 250 mL tungsten carbide grinding jar was loaded with 150 mL of tungsten carbide balls and 85 mL of RH. It was milled for 2 h at 400 rpm; this was done to achieve homogenous particles size.
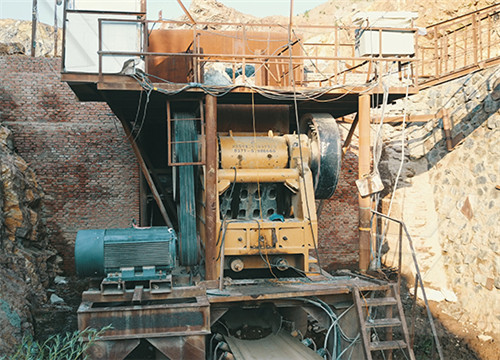
Process optimization of a chrome ore gravity
> Concentration (classification and beneficiation). The beneficiation process flow sheet varies from location to location according to the ore characteristics. For example, the Kemi concentrator in Finland comprises
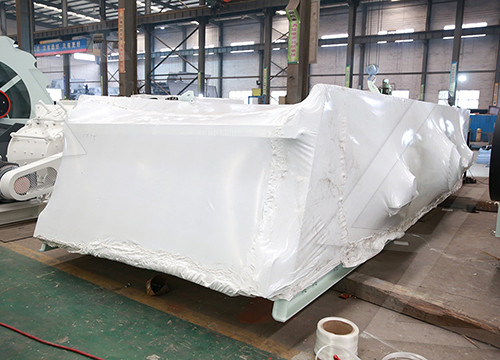
A facile approach to synthesis of silica nanoparticles from silica
2.1. Materials. The raw material used to produce silica nanoparticles was supplied from silica sand on Belitung Island, Indonesia. According to X-ray fluorescence (XRF) analysis, the SiO 2 concentration of silica sand is about 99.42%. All the chemicals used were nitric acid, hydrochloric acid, sodium hydroxide, methanol, ethanol, and 2-propanol, purchased from
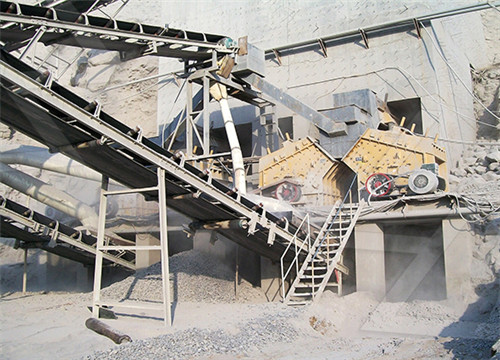
Effects of slurry concentration and powder filling on the net mill
20031115 The tests covered a range of slurry concentrations from 30 to 55 vol.% solid and fractional interstitial bed filling (U) from 0.3 to 1.75, at a fixed ball load (30% of mill volume) and 70% of critical speed, using batch grinding of a feed of −30 mesh (0.6 mm) quartz.At a fixed slurry concentration, the net mill power versus U went through a
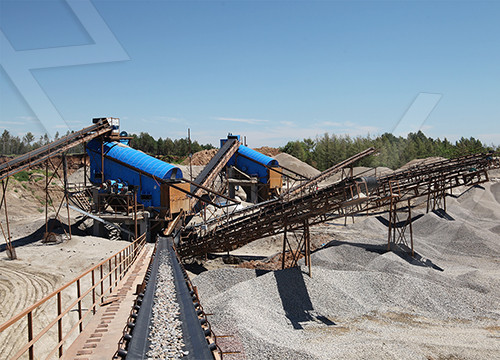
Evolution of grinding energy and particle size during dry ball
2020101 In this , we present a detailed investigation of the dry grinding of silica sand in an oscillatory ball mill. We are interested in the evolution of specific surface area (SSA), particle size distribution, agglomerated SSA and consumed electrical energy as a function of the input grinding energy power.
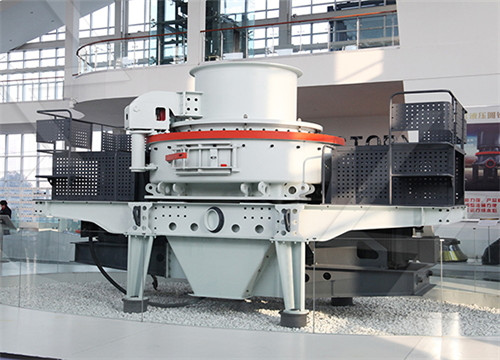
Evolution of grinding energy and particle size during dry ball
2020101 Fig. 1 a shows the oscillatory ball mill (Retsch® MM400) used in this study and a scheme (Fig. 1 b) representing one of its two 50 mL milling jars. Each jar is initially filled with a mass M of raw material and a single 25 mm-diameter steel ball. The jars vibrate horizontally at a frequency chosen between 3 and 30 Hz. The motion of the jar follows a
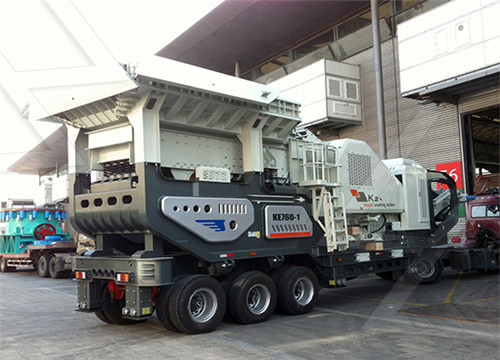
Dispersion of amorphous silica nanoparticles via beads
202011 The contact angle measurement of the dispersed silica reveals the superior hydrophobic behaviour of SiO 2, especially with 10 wt% SND 504 dispersing agent. The critical surface tension of SiO 2 with 10 wt% SND 504 dispersing agent reveal low value compared to other concentration of dispersant. Thus, the dispersed silica nanoparticles
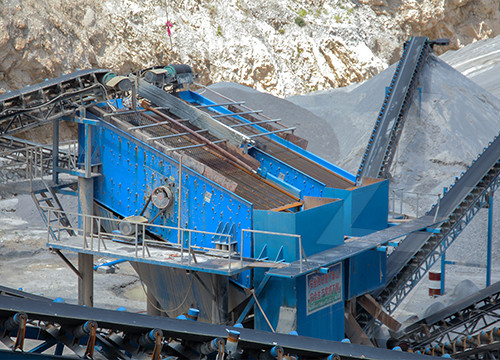
How Ball Mill Ore Feed Size Affects TonnageCapacity
2017726 Hard ore Work Index 16 = 100,000/65,000 = 1.54 kwh/t. For the purposes of this example, we will hypothesize that the the crushing index of the hard ore with the increased energy input of 1.54 kw/t reduces the ball mill feed size to 6,500 micrometers. As a result, the mill output will increase with this reduced size to approximately 77,000 tons