أرسل لنا رسالة
iron ore grinding ball mill process chart

Ball Grinding Process SpringerLink
2023727 Download reference work entry PDF. Ball grinding process is a grinding method of crushing ore with ball-shaped grinding medium in the grinding mill. In the ball
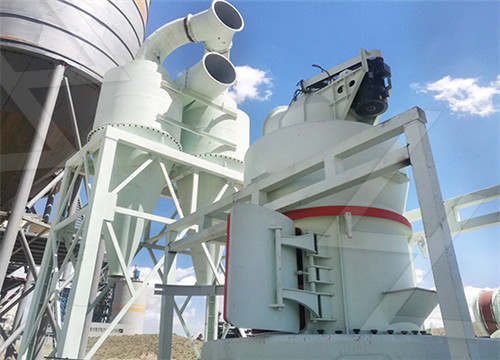
The six main steps of iron ore processing Multotec
Six steps to process iron ore 1. Screening We recommend that you begin by screening the iron ore to separate fine particles below the crusher’s CSS before the crushing stage. A
Iron Ore Processing Flowsheet Multotec6 Stages of the Mining Process BOSS Magazine:Iron Ore Processing Flow ChartIron Ore To Steel ProcessMultotec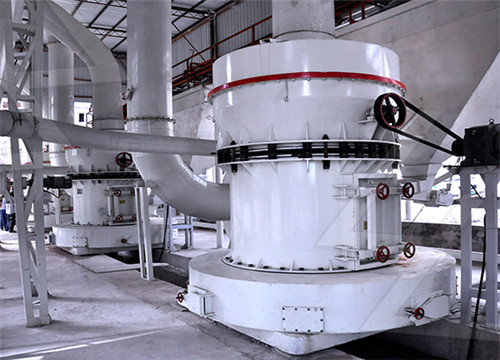
(PDF) Grinding Media in Ball Mills-A Review
2023423 International Journal of Mineral Processing. Farit Urakaev. We will focus on the important aspect of mechanochemical processing by grinding in a ball mill, namely, nanoscale wear of the treated
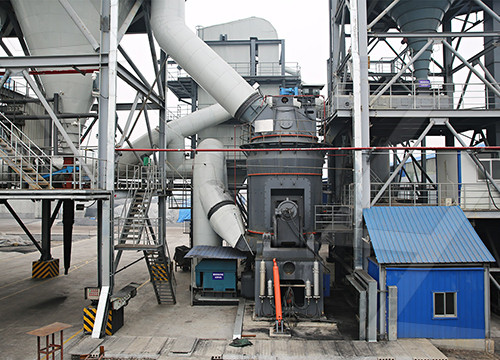
Mechanistic modeling and simulation of grinding iron ore
2021111 Based on the machine learning method, this study analyzed the full process parameters (i.e., ball mill power, fresh ore feed rate, hydrocyclone feed pump
: Rodrigo M. de Carvalho, Tulio M. Campos, Patricia M. Faria, Patricia M. Faria, Luís Marcelo Tavares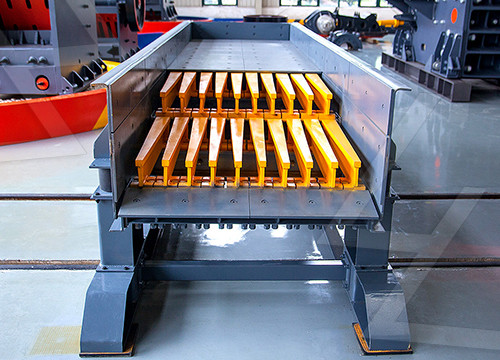
Optimization of Solids Concentration in Iron Ore Ball Milling
2019618 The stone demonstrates the application of this methodology to optimize solids concentration in ball milling of an iron ore from Brazil. The wet grinding
: Patricia M. C. Faria, Raj K. Rajamani, Luís M. Tavares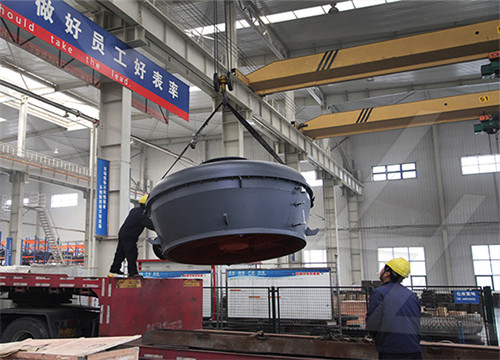
Development of a Novel Grinding Process to Iron Ore
2020328 Modern iron ore pelletizing process operations may be divided into two main process sections: feedstock preparation and agglomeration processes. In most
:MillIron OrePublish Year:2020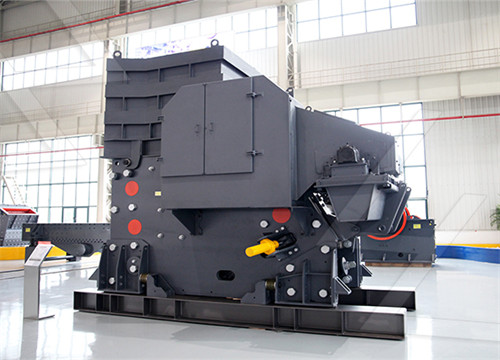
Estimation of Grinding Time for Desired Particle Size
202013 The grinding process for all the three iron ores is carried out individually in Bond’s ball mill and the total retention time taken by each iron ore sample is calculated.
:MillIron OrePublish Year:2020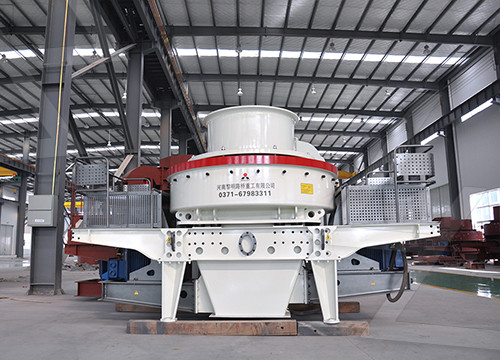
(PDF) Evaluation of grinding circuits for iron ore
201931 The aim of this study was to evaluate and compare two grinding circuits in an industrial iron ore plant, by evaluating the current operation through sampling,
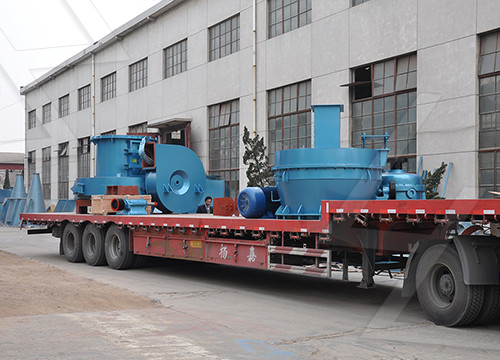
The Effect of Grinding Media on Mineral Breakage
20211211 The breakage and liberation of minerals are the key to fluidized mining for minerals. In the ball milling process, steel balls function as not only a grinding action implementer but also energy carrier to
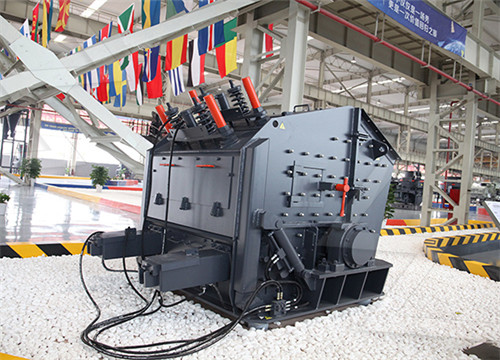
A Review of the Grinding Media in Ball Mills for Mineral
20231027 The ball mill is a rotating cylindrical vessel with grinding media inside, which is responsible for breaking the ore particles. Grinding media play an important role
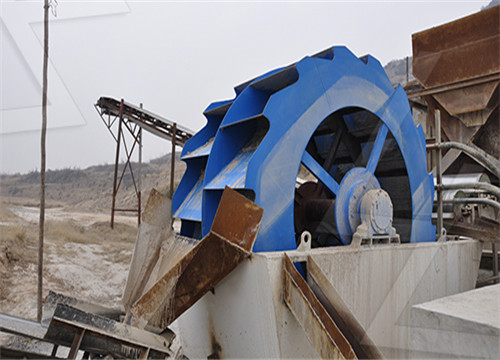
Feed hardness and acoustic emissions of autogenous/semi
202291 For all grind times, the acoustical levels of the iron ore grinding behaviour were observed to be typically between those of Feature extraction and selection based on vibration spectrum with application to estimating the load parameters of ball mill in grinding process. Control Eng. Pract., 20 (10) (2012), pp. 991-1004. View PDF View
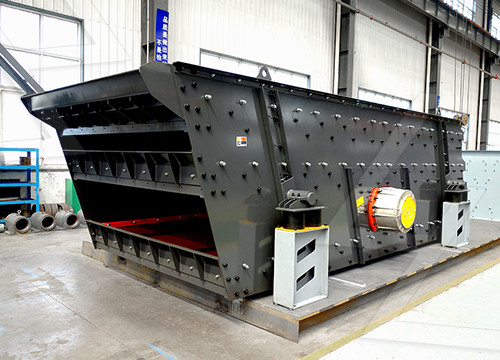
Research of iron ore grinding in a vertical-roller-mill
2015315 The application of vertical-roller-mills (VRM’s) for ore grinding is part of the second strategy. The grinding parts of a Loesche mill ( Fig. 1) are a rotating table (1) with a horizontal grinding track and rollers (2), which are pressed onto the table by lever arms and a hydro pneumatic spring system.
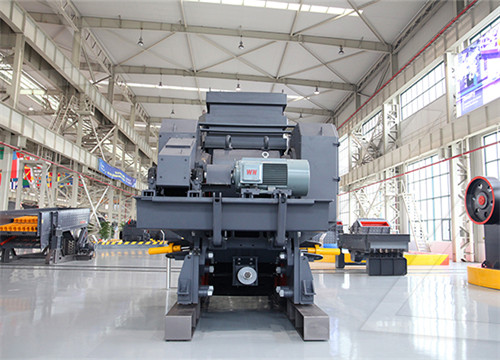
Procedure for determination of ball Bond work index in the
200911 Section snip Grinding kinetics in the Bond ball mill. Tests of grinding kinetics in the Bond ball mill (Fig. 1, Fig. 2) has shown that over a shorter grinding period, the process follows the law of first order kinetics R = R 0 e-kt where R = test-sieve oversize at the time (t); R 0 = test sieve at the beginning of grinding (t = 0); k: grinding rate
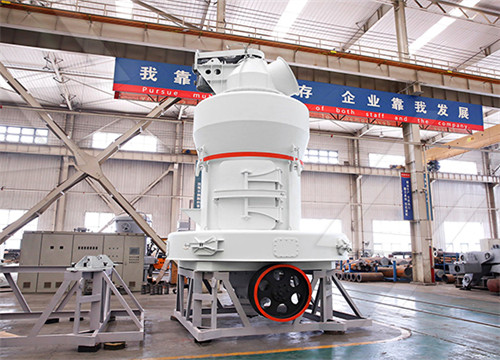
A discussion on the measurement of grinding media wear
201671 The grinding media may be the ore itself (autogenous grinding), bars, balls, or cylpebs, or even the ore itself together with a small amount of balls (semi-autogenous grinding). A survey found out that approximately 53% of the grinding circuits around the world use ball mills, and 38% use autogenous or semi-autogenous grinding, and
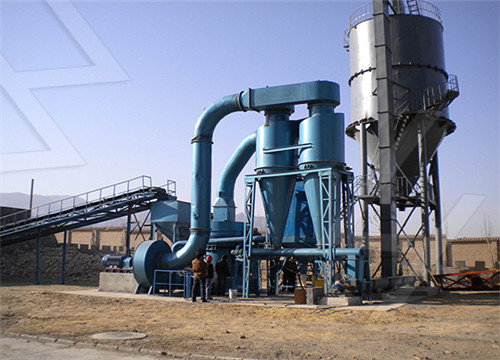
11.6 Portland Cement Manufacturing US EPA
1971817 In the wet process, water is added to the raw mill during the grinding of the raw materials in ball or tube mills, thereby producing a pumpable slurry, or slip, of approximately 65 percent solids. The slurry is agitated, blended, and stored in various kinds and sizes of cylindrical tanks or slurry basins until it is fed to the pyroprocessing
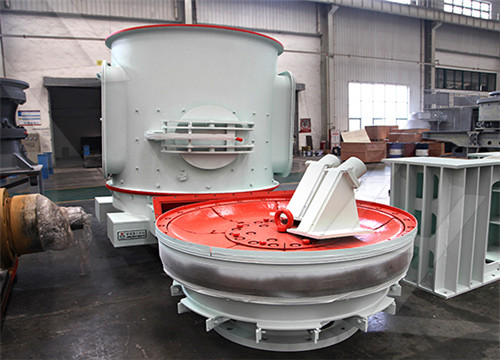
Investigation on Iron Ore Grinding based on Particle Size Distribution
2020528 The feed samples of X, Y, and Z iron ores were ground in the BBM (ball mill refers to a BBM of size 300 mm × 300 mm with smooth liners) to identify the PSD, BWI, and RT of each ore. Grinding experiments were conducted according to Bond’s standard test procedure [].For each iron ore sample, the RT taken to produce 250% circulating
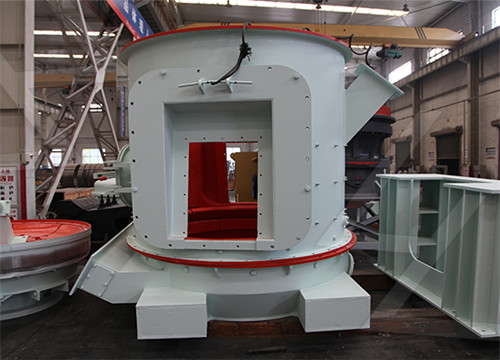
Bond Work Index an overview ScienceDirect Topics
The ball mill work index laboratory test is conducted by grinding an ore sample prepared to 100% passing 3.36 mm (6 mesh) to product size in the range of 45-150 µm (325-100 mesh), thus determining the ball mill work index (Wi B or BWi). The work index calculations across a narrow size range are conducted using the appropriate laboratory work

Iron Ore Processing, General SpringerLink
20221020 Iron ore handling, which may account for 20–50% of the total delivered cost of raw materials, covers the processes of transportation, storage, feeding, and washing of the ore en route to or during its various stages of treatment in the mill.. Since the physical state of iron ores in situ may range from friable, or even sandy materials, to monolithic
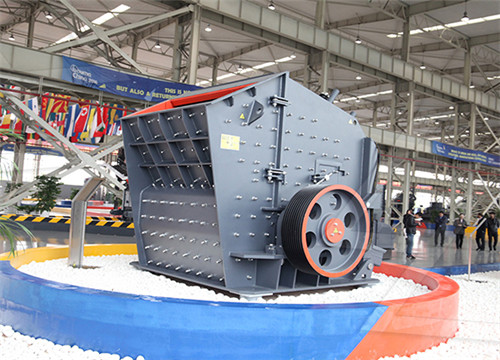
Copper Processing Multotec
Thereafter, the oversized ore is sent to the SAG mill. A hammer sampler is used to sample the feed and an overbelt magnet is used to remove any tramp iron from the feed, before going to the SAG mill. The underflow is sent to a secondary ball mill and trommel screen, Typical Copper Extraction Process Flow Chart (Copper Oxide): Multotec

The Effect of Grinding Media on Mineral Breakage Properties
20211211 The breakage and liberation of minerals are the key to fluidized mining for minerals. In the ball milling process, steel balls function as not only a grinding action implementer but also energy carrier to determine the breakage behavior of ores and the production capacity of the mill. When ground products present a much coarse or much

Ball Mill an overview ScienceDirect Topics
Quantum Nanostructures (QDs): An Overview. D. Sumanth Kumar, H.M. Mahesh, in Synthesis of Inorganic Nanomaterials, 2018 3.6.1.1 Ball Milling. A ball mill is a type of grinder used to grind and blend bulk material into QDs/nanosize using different sized balls. The working principle is simple; impact and attrition size reduction take place as the ball
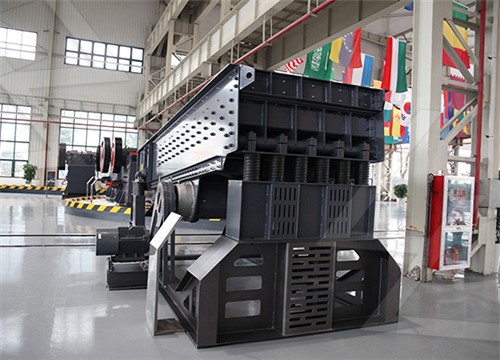
Optimizing heat treatment and wear resistance of high
2011729 The properties of the metallic matrix are fundamental to obtain high wear resistance. The example shown in Fig. 1 refers to cast irons tested as grinding balls in a ball mill [2].Because of different heat treatments one sample has high hardness martensitic matrix while the other presents a low hardness austenitic matrix.
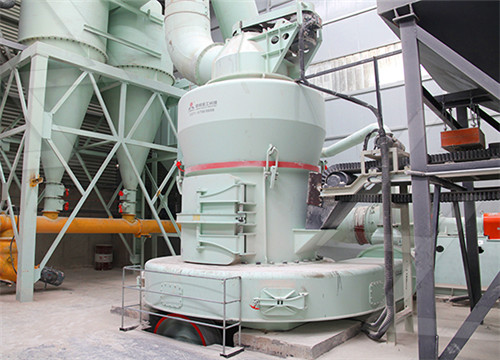
Methods of Ore Pretreatment for Comminution Energy
202043 The machine could process ore up to 10 th −1 (3–10 th −1), depending on the pulse energy, PSD, and density of the ore. The PSDs of the tested ores were 22.4–26.5, 31.5–37.5, and 45–53 mm. The developed device and ball mill were used separately for the grinding of prepared copper ore feeds. Effect of thermal treatment via
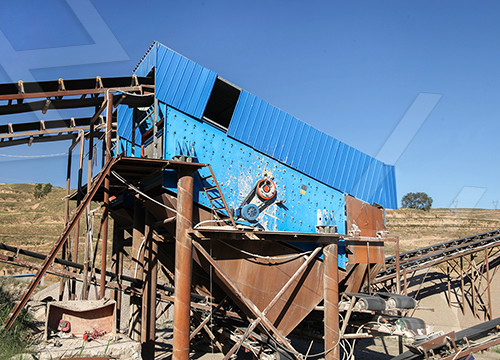
Flow chart of lithium ore crushing, grinding and screening process
20221227 The steel ball (or iron ball) grinding machine is the ball mill; Steel rod for rod mill; The gravel is loaded by a gravel mill. If there is no other medium in the mill, only the use of ore grinding, it is called mediumless mill or self-grinding machine; Autogenous mill and add the right amount of steel ball to form the so-called semi-autogenous
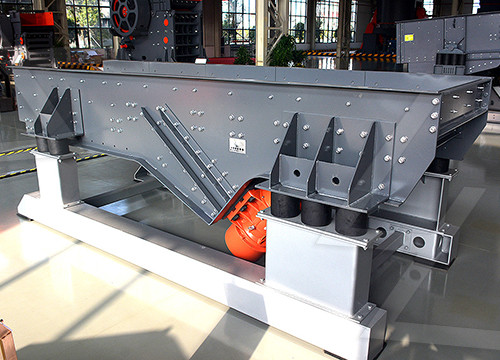
Standard Grindability Tests and Calculations 911
201641 periods, and this is recorded as the grind- ability, or relative ease of grinding, of the sample. A cylindrical ball mill, 12 by 12 in. inside, with a smooth lining and rounde.1 corners, is used with a revolution counter Under standard grinding conditions it runs at 70 r.p.m., and contains a charge oi 285 iron balls weighing 20,125 grams,
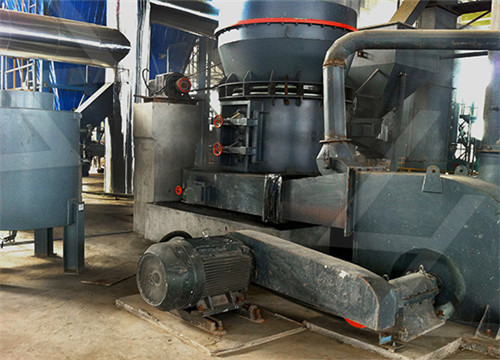
Mineral processing milling
201588 Iron Ore 0.20 Lime (industrial applications such as detergents) 0.10 China clay 0.002 Alumina 0.005 Table 3: Material Particle Size Characteristics of Mills Types of mills In this brief we categorise mills in 3 groups: 1. Low-speed tumbling mills 2. Roller mills 3. Very fine grinding mills, which include the following types of mill:
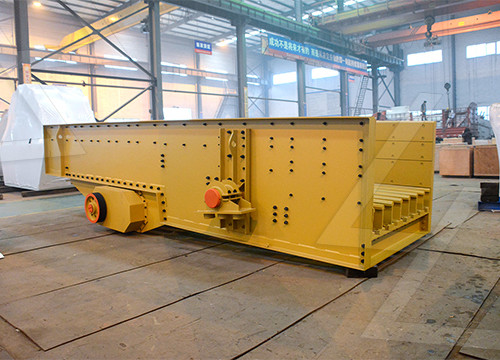
Optimal-Setting for Ore and Water Feeding in Grinding Process
2021623 The grinding product particle size is the most crucial operational index of mineral grinding processes. The size and consistency of the product directly affects the subsequent dressing and sintering. In this , a novel expert system is proposed for guiding the operating variables to keep the product stable with the wildly varying ore
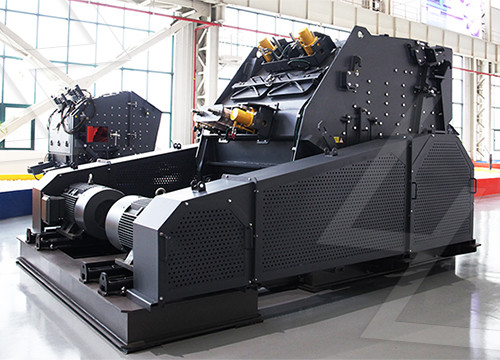
Summary of Gold Plants and Processes ScienceDirect
201611 Table 54.1. Summary of Gold Plants and Flow Sheets Discussed in Gold Ore Processing, Second Edition. Implemented with tube autoclaves 1.5 km long and 5 cm inner diameter. Leaching at ambient temperature and 5 MPa oxygen pressure and 0.2–0.5% NaCN; 15 min residence time for 85% recovery.
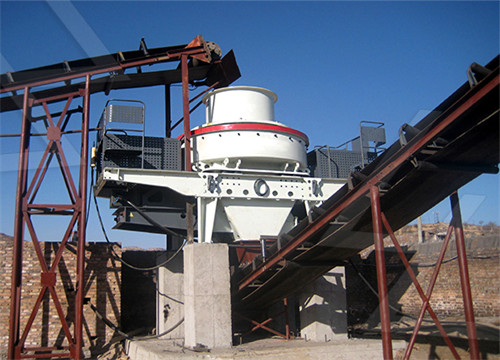
An innovative approach for determining the grinding media
2021122 The grinding experiment was operated with the Anshan type iron ore. The results of the laboratory grinding experiment indicated that the media size ratio, space-filling factor, and material ball ratio had a significant influence on the grinding kinetics of the iron ore sample. (2) The average grinding rate increased with a decrease in media size.
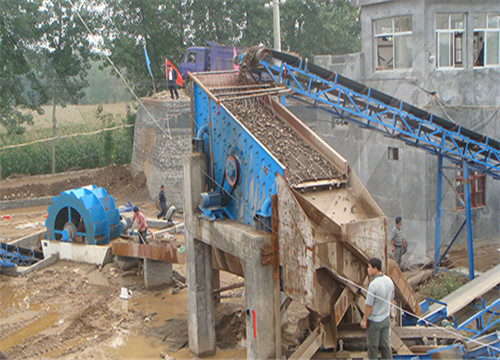
schematic flow chart of a crushing and grinding mill GitHub
Closed Circuit Grinding VS Open Circuit Grinding 911 Metallurgist. Mar 17,2017.The simplest grinding circuit consists of a ball or rod mill in closed circuit with a classifier; the flow sheet is shown in Fig.found very useful in plants in which improvements in dry crushing practice have resulted in a reduction.
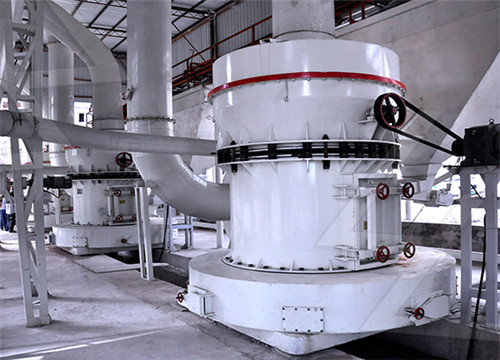
(PDF) Grinding Media in Ball Mills-A Review
2023423 International Journal of Mineral Processing. Farit Urakaev. We will focus on the important aspect of mechanochemical processing by grinding in a ball mill, namely, nanoscale wear of the treated
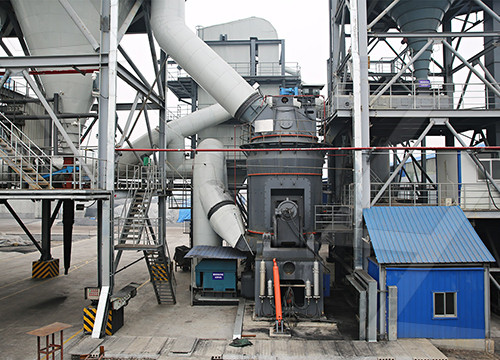
Mechanistic modeling and simulation of grinding iron ore
2021111 Based on the machine learning method, this study analyzed the full process parameters (i.e., ball mill power, fresh ore feed rate, hydrocyclone feed pump
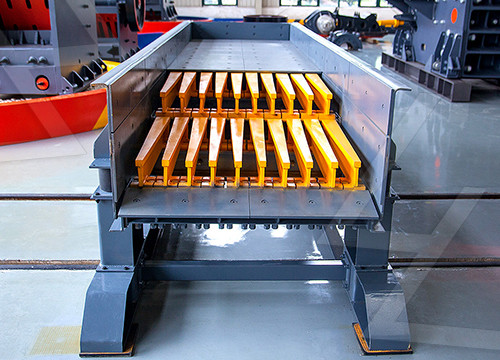
Optimization of Solids Concentration in Iron Ore Ball Milling
2019618 The stone demonstrates the application of this methodology to optimize solids concentration in ball milling of an iron ore from Brazil. The wet grinding
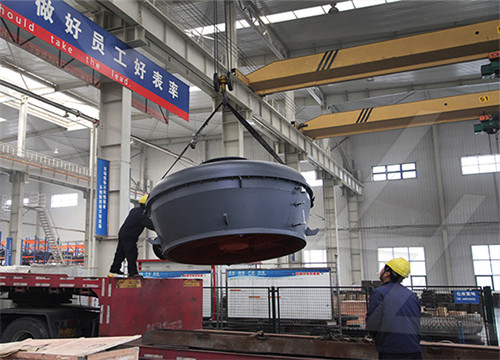
Development of a Novel Grinding Process to Iron Ore
2020328 Modern iron ore pelletizing process operations may be divided into two main process sections: feedstock preparation and agglomeration processes. In most
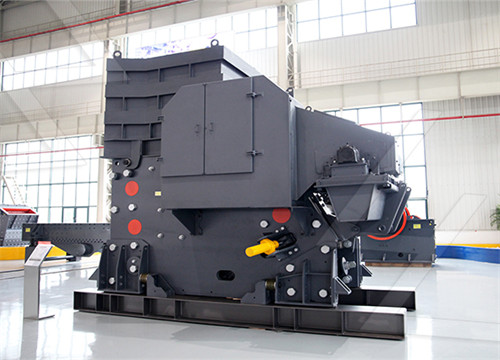
Estimation of Grinding Time for Desired Particle Size
202013 The grinding process for all the three iron ores is carried out individually in Bond’s ball mill and the total retention time taken by each iron ore sample is calculated.
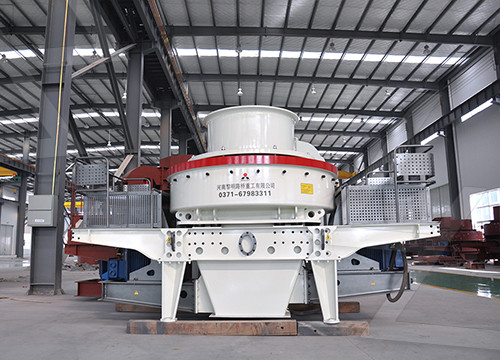
(PDF) Evaluation of grinding circuits for iron ore
201931 The aim of this study was to evaluate and compare two grinding circuits in an industrial iron ore plant, by evaluating the current operation through sampling,
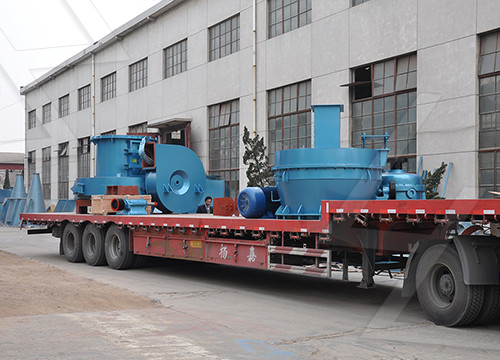
The Effect of Grinding Media on Mineral Breakage
20211211 The breakage and liberation of minerals are the key to fluidized mining for minerals. In the ball milling process, steel balls function as not only a grinding action implementer but also energy carrier to
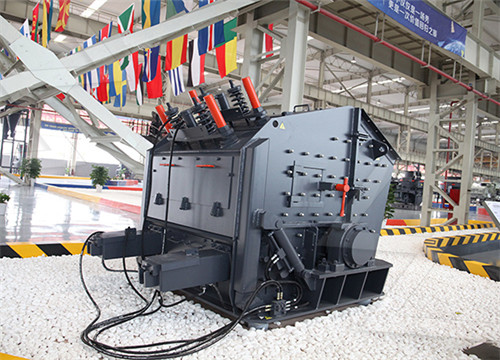
A Review of the Grinding Media in Ball Mills for Mineral
20231027 The ball mill is a rotating cylindrical vessel with grinding media inside, which is responsible for breaking the ore particles. Grinding media play an important role
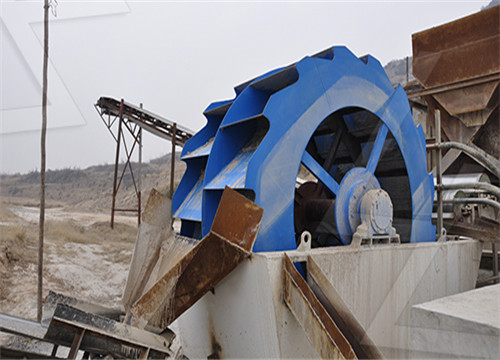
Feed hardness and acoustic emissions of autogenous/semi
202291 For all grind times, the acoustical levels of the iron ore grinding behaviour were observed to be typically between those of Feature extraction and selection based on vibration spectrum with application to estimating the load parameters of ball mill in grinding process. Control Eng. Pract., 20 (10) (2012), pp. 991-1004. View PDF View
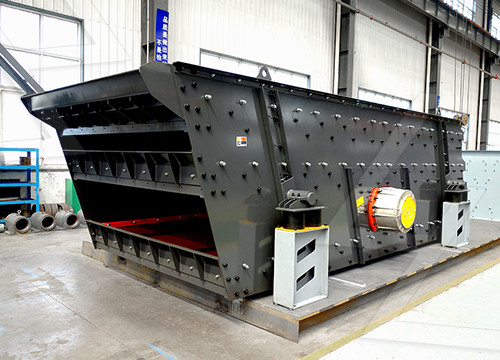
Research of iron ore grinding in a vertical-roller-mill
2015315 The application of vertical-roller-mills (VRM’s) for ore grinding is part of the second strategy. The grinding parts of a Loesche mill ( Fig. 1) are a rotating table (1) with a horizontal grinding track and rollers (2), which are pressed onto the table by lever arms and a hydro pneumatic spring system.
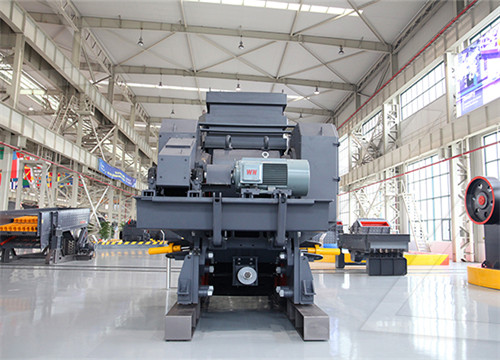
Procedure for determination of ball Bond work index in the
200911 Section snip Grinding kinetics in the Bond ball mill. Tests of grinding kinetics in the Bond ball mill (Fig. 1, Fig. 2) has shown that over a shorter grinding period, the process follows the law of first order kinetics R = R 0 e-kt where R = test-sieve oversize at the time (t); R 0 = test sieve at the beginning of grinding (t = 0); k: grinding rate
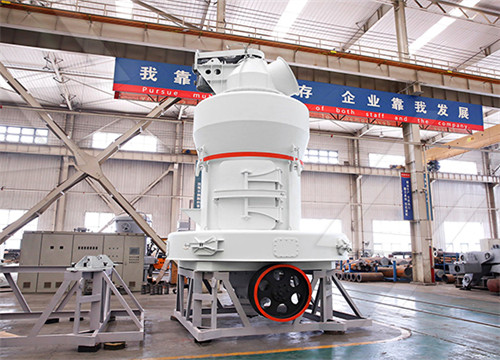
A discussion on the measurement of grinding media wear
201671 The grinding media may be the ore itself (autogenous grinding), bars, balls, or cylpebs, or even the ore itself together with a small amount of balls (semi-autogenous grinding). A survey found out that approximately 53% of the grinding circuits around the world use ball mills, and 38% use autogenous or semi-autogenous grinding, and
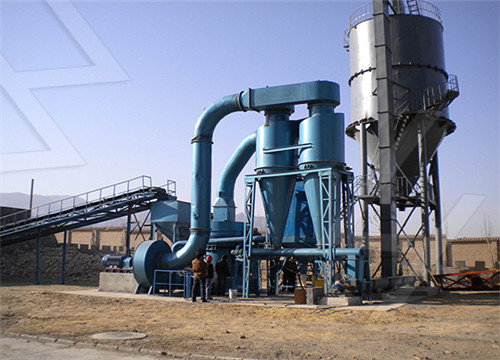
11.6 Portland Cement Manufacturing US EPA
1971817 In the wet process, water is added to the raw mill during the grinding of the raw materials in ball or tube mills, thereby producing a pumpable slurry, or slip, of approximately 65 percent solids. The slurry is agitated, blended, and stored in various kinds and sizes of cylindrical tanks or slurry basins until it is fed to the pyroprocessing
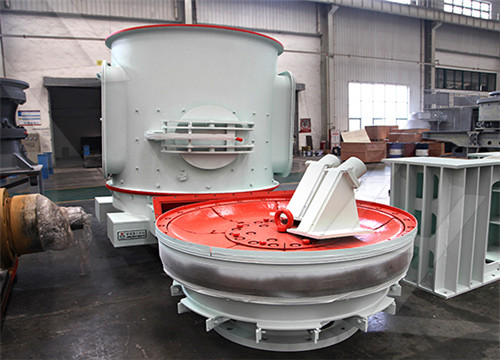
Investigation on Iron Ore Grinding based on Particle Size Distribution
2020528 The feed samples of X, Y, and Z iron ores were ground in the BBM (ball mill refers to a BBM of size 300 mm × 300 mm with smooth liners) to identify the PSD, BWI, and RT of each ore. Grinding experiments were conducted according to Bond’s standard test procedure [].For each iron ore sample, the RT taken to produce 250% circulating
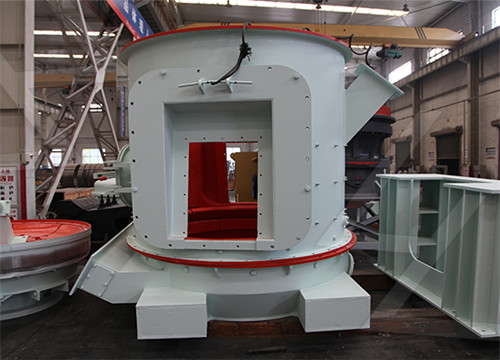
Bond Work Index an overview ScienceDirect Topics
The ball mill work index laboratory test is conducted by grinding an ore sample prepared to 100% passing 3.36 mm (6 mesh) to product size in the range of 45-150 µm (325-100 mesh), thus determining the ball mill work index (Wi B or BWi). The work index calculations across a narrow size range are conducted using the appropriate laboratory work

Iron Ore Processing, General SpringerLink
20221020 Iron ore handling, which may account for 20–50% of the total delivered cost of raw materials, covers the processes of transportation, storage, feeding, and washing of the ore en route to or during its various stages of treatment in the mill.. Since the physical state of iron ores in situ may range from friable, or even sandy materials, to monolithic
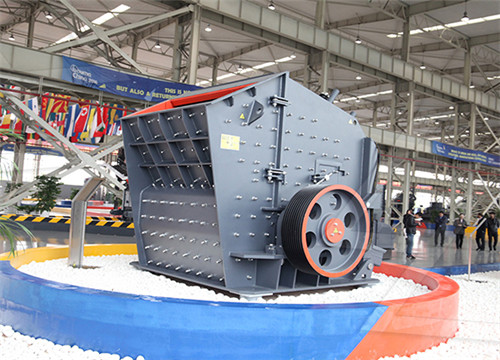
Copper Processing Multotec
Thereafter, the oversized ore is sent to the SAG mill. A hammer sampler is used to sample the feed and an overbelt magnet is used to remove any tramp iron from the feed, before going to the SAG mill. The underflow is sent to a secondary ball mill and trommel screen, Typical Copper Extraction Process Flow Chart (Copper Oxide): Multotec

The Effect of Grinding Media on Mineral Breakage Properties
20211211 The breakage and liberation of minerals are the key to fluidized mining for minerals. In the ball milling process, steel balls function as not only a grinding action implementer but also energy carrier to determine the breakage behavior of ores and the production capacity of the mill. When ground products present a much coarse or much

Ball Mill an overview ScienceDirect Topics
Quantum Nanostructures (QDs): An Overview. D. Sumanth Kumar, H.M. Mahesh, in Synthesis of Inorganic Nanomaterials, 2018 3.6.1.1 Ball Milling. A ball mill is a type of grinder used to grind and blend bulk material into QDs/nanosize using different sized balls. The working principle is simple; impact and attrition size reduction take place as the ball
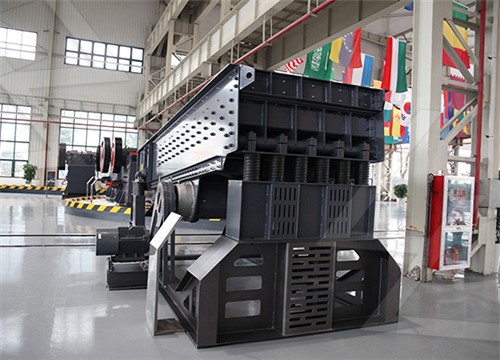
Optimizing heat treatment and wear resistance of high
2011729 The properties of the metallic matrix are fundamental to obtain high wear resistance. The example shown in Fig. 1 refers to cast irons tested as grinding balls in a ball mill [2].Because of different heat treatments one sample has high hardness martensitic matrix while the other presents a low hardness austenitic matrix.
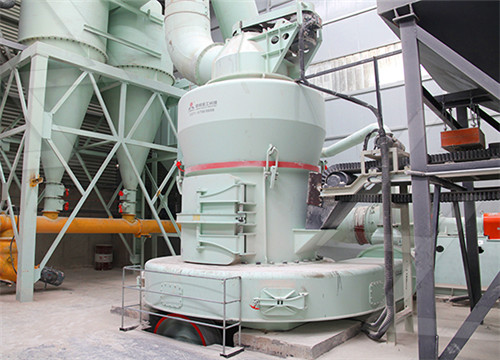
Methods of Ore Pretreatment for Comminution Energy
202043 The machine could process ore up to 10 th −1 (3–10 th −1), depending on the pulse energy, PSD, and density of the ore. The PSDs of the tested ores were 22.4–26.5, 31.5–37.5, and 45–53 mm. The developed device and ball mill were used separately for the grinding of prepared copper ore feeds. Effect of thermal treatment via
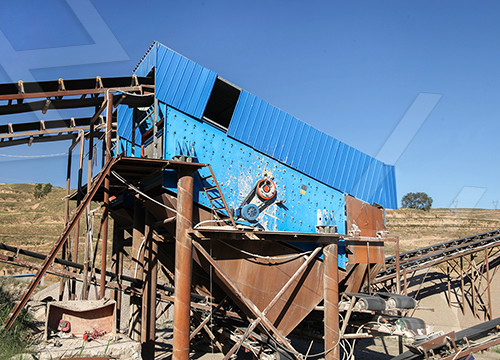
Flow chart of lithium ore crushing, grinding and screening process
20221227 The steel ball (or iron ball) grinding machine is the ball mill; Steel rod for rod mill; The gravel is loaded by a gravel mill. If there is no other medium in the mill, only the use of ore grinding, it is called mediumless mill or self-grinding machine; Autogenous mill and add the right amount of steel ball to form the so-called semi-autogenous
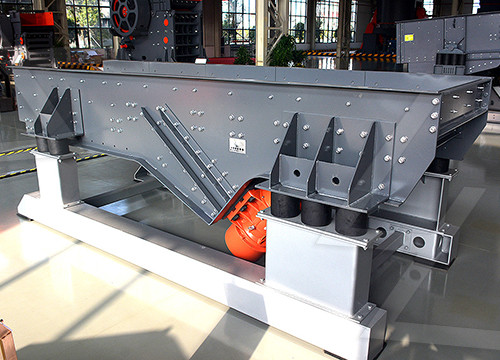
Standard Grindability Tests and Calculations 911
201641 periods, and this is recorded as the grind- ability, or relative ease of grinding, of the sample. A cylindrical ball mill, 12 by 12 in. inside, with a smooth lining and rounde.1 corners, is used with a revolution counter Under standard grinding conditions it runs at 70 r.p.m., and contains a charge oi 285 iron balls weighing 20,125 grams,
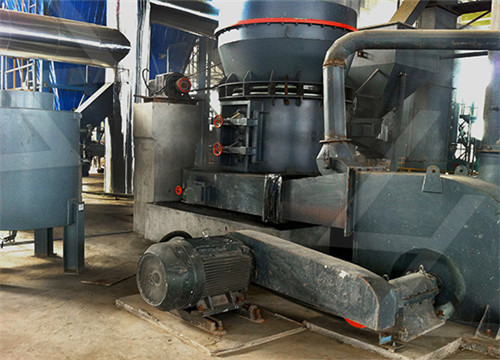
Mineral processing milling
201588 Iron Ore 0.20 Lime (industrial applications such as detergents) 0.10 China clay 0.002 Alumina 0.005 Table 3: Material Particle Size Characteristics of Mills Types of mills In this brief we categorise mills in 3 groups: 1. Low-speed tumbling mills 2. Roller mills 3. Very fine grinding mills, which include the following types of mill:
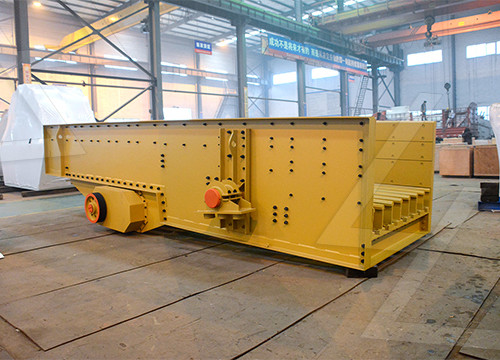
Optimal-Setting for Ore and Water Feeding in Grinding Process
2021623 The grinding product particle size is the most crucial operational index of mineral grinding processes. The size and consistency of the product directly affects the subsequent dressing and sintering. In this , a novel expert system is proposed for guiding the operating variables to keep the product stable with the wildly varying ore
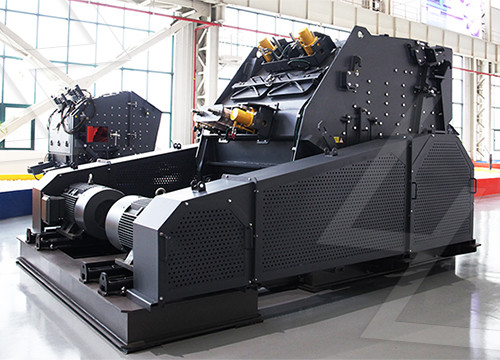
Summary of Gold Plants and Processes ScienceDirect
201611 Table 54.1. Summary of Gold Plants and Flow Sheets Discussed in Gold Ore Processing, Second Edition. Implemented with tube autoclaves 1.5 km long and 5 cm inner diameter. Leaching at ambient temperature and 5 MPa oxygen pressure and 0.2–0.5% NaCN; 15 min residence time for 85% recovery.
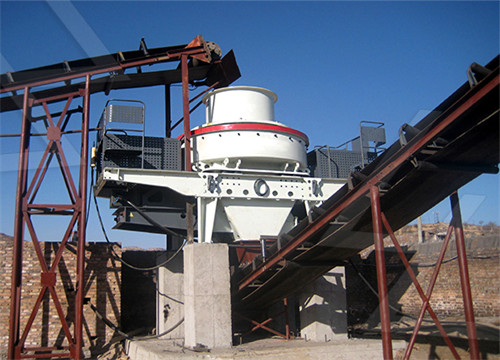
An innovative approach for determining the grinding media
2021122 The grinding experiment was operated with the Anshan type iron ore. The results of the laboratory grinding experiment indicated that the media size ratio, space-filling factor, and material ball ratio had a significant influence on the grinding kinetics of the iron ore sample. (2) The average grinding rate increased with a decrease in media size.
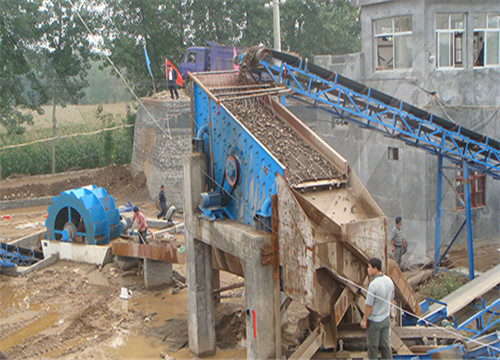
schematic flow chart of a crushing and grinding mill GitHub
Closed Circuit Grinding VS Open Circuit Grinding 911 Metallurgist. Mar 17,2017.The simplest grinding circuit consists of a ball or rod mill in closed circuit with a classifier; the flow sheet is shown in Fig.found very useful in plants in which improvements in dry crushing practice have resulted in a reduction.